Does alloy steel break easily?
Have you ever wondered about the strength of the materials that make up the cars we drive, the planes we fly in, and the bridges we cross every day? Alloy steel is a common material used in many of these applications, but how strong is it really? Let me share with you a story of a bridge collapse that sparked a debate about the strength of alloy steel. In 1940, the Tacoma Narrows Bridge in Washington state famously collapsed due to a phenomenon known as “flutter,” where strong winds caused the bridge to vibrate and eventually break apart. Many people blamed the use of alloy steel for the collapse, questioning its ability to withstand strong forces. But is it fair to blame the material? Can alloy steel break easily?
No, alloy steel is designed to have high strength and toughness, making it resistant to breakage even under significant stress or impact. Its unique composition of multiple metals also helps to increase its durability and resistance to corrosion, making it a popular material for various industrial applications.
Let’s dive deeper into the properties of alloy steel and find out if it really breaks easily.
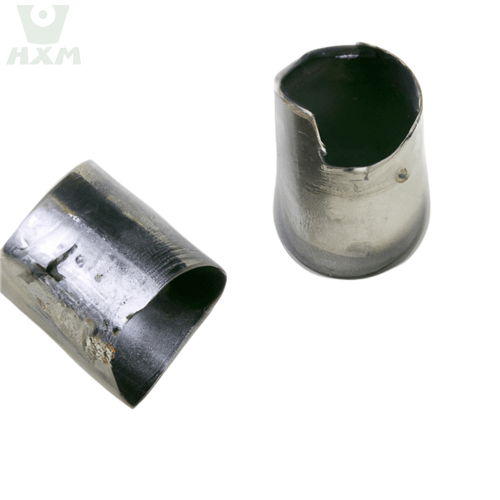
I. Introduction
A. Explanation of what alloy steel is
Alloy steel is a type of steel that contains additional elements such as nickel, chromium, or molybdenum to improve its properties such as strength, durability, and corrosion resistance. These additional elements are added in specific proportions to create a desired alloy with unique properties.
B. Background on the topic of alloy steel breaking
Alloy steel is commonly used in applications where strength is critical, such as in construction, manufacturing, and engineering. However, there have been instances where alloy steel has broken or failed, leading to concerns about its reliability and safety.
C. Importance of understanding the strength of alloy steel
Understanding the strength and toughness of alloy steel is crucial for ensuring its reliability and safety in various applications. By understanding the factors that affect the strength of alloy steel and how it responds to different types of stresses, we can design and use alloy steel in a way that minimizes the risk of failure. In this article, we will explore the factors that can cause alloy steel to break, as well as preventative measures and repair methods to mitigate this risk.
By Huaxia-steel – Alloy Steel Suppliers
II. Understanding Alloy Steel
A. Properties of steel alloys
Steel alloys are made by combining iron with other elements, such as carbon, manganese, chromium, and nickel. The properties of steel alloys can be tailored to meet specific needs by adjusting the chemical composition and manufacturing process. Steel alloys are known for their high strength, toughness, and resistance to wear and tear. They are also ductile, which means they can be easily shaped or molded without breaking.
B. Different types of alloy steel
There are many different types of alloy steel, each with its own unique properties and uses. Some common types of alloy steel include:
- Carbon steel – This is a type of alloy steel that contains high amounts of carbon, typically between 0.6% and 1.5%. Carbon steel is known for its high strength and hardness, but it can be brittle and prone to breaking.
- Stainless steel – This is a type of alloy steel that contains at least 10.5% chromium, which provides excellent corrosion resistance. Stainless steel is commonly used in applications where resistance to corrosion and staining is important, such as in the food industry and medical equipment.
- Tool steel – This is a type of alloy steel that is designed to be used in the production of tools, dies, and molds. Tool steel is typically hardened and tempered to provide high strength and wear resistance.
C. Applications of alloy steel
Alloy steel is used in a wide range of applications, including construction, automotive manufacturing, aerospace, and industrial equipment. It is commonly used in the production of structural components, such as beams and girders, as well as in the production of machinery parts and tools. Alloy steel is also used in the production of pipes, valves, and other components for the oil and gas industry.
By Huaxia-steel – Alloy Steel Suppliers
III. Strength and Toughness of Alloy Steel
A. Explanation of strength and toughness
Strength and toughness are two important properties that determine the ability of alloy steel to resist breaking. Strength refers to the amount of stress a material can withstand before it breaks, while toughness refers to the ability of the material to absorb energy before fracturing.
B. The relationship between strength and toughness
In general, materials with high strength tend to have low toughness, and vice versa. However, there are some alloy steels that are able to achieve high levels of both strength and toughness through careful selection of alloying elements and heat treatment processes.
C. Factors that affect strength and toughness of alloy steel
Several factors can affect the strength and toughness of alloy steel, including:
- Chemical composition – The type and amount of alloying elements used can significantly impact the strength and toughness of the steel. For example, adding elements such as chromium and molybdenum can increase strength and corrosion resistance, while adding nickel can improve toughness.
- Heat treatment – The heat treatment process can also greatly affect the properties of alloy steel. Processes like quenching and tempering can improve strength, while annealing can improve toughness.
- Microstructure – The size, shape, and distribution of the steel’s microstructure can affect its strength and toughness. For example, a fine-grained microstructure can lead to improved toughness.
- Surface finish – The surface finish of the steel can also impact its strength and toughness. Rough surfaces can create stress concentration points that can lead to failure.
D. Differences between brittle and ductile materials
Brittle materials, such as glass, are prone to sudden and catastrophic failure when subjected to stress. Ductile materials, on the other hand, are able to deform and absorb energy before fracturing. Alloy steel can exhibit both brittle and ductile behavior depending on its composition and processing.
E. Common tests used to measure strength and toughness of alloy steel
Several tests are commonly used to measure the strength and toughness of alloy steel, including tensile tests, impact tests, and hardness tests. These tests can provide valuable information for material selection and design in applications where strength and toughness are critical factors.
By Huaxia-steel – Alloy Steel Suppliers
IV. Factors that Affect Alloy Steel's Ability to Resist Breaking
Alloy steel is widely used in various industries because of its high strength and toughness. However, the ability of alloy steel to resist breaking depends on several factors. Understanding these factors is crucial in selecting the appropriate type of alloy steel for specific applications and ensuring its reliable performance. Here are some of the factors that affect the ability of alloy steel to resist breaking:
A. Chemical composition of alloy steel
The chemical composition of alloy steel greatly affects its strength and toughness. Adding different elements to the steel changes its properties, making it more suitable for specific applications. For instance, adding chromium to steel increases its corrosion resistance and strength, while adding molybdenum improves its toughness at high temperatures. Therefore, it is essential to consider the chemical composition of alloy steel when selecting it for specific applications.
B. Heat treatment process
Heat treatment is an essential process for improving the properties of alloy steel. It involves heating the steel to a specific temperature and then cooling it at a specific rate. The heat treatment process affects the microstructure of the steel, which greatly impacts its strength and toughness. For example, quenching and tempering increase the strength and toughness of alloy steel, making it suitable for high-stress applications. On the other hand, annealing reduces the strength and hardness of alloy steel, making it more ductile and suitable for applications that require bending or forming.
C. Microstructure of alloy steel
The microstructure of alloy steel affects its mechanical properties, such as strength, toughness, and ductility. The microstructure of steel can be controlled through the heat treatment process and the chemical composition of the steel. A fine and uniform microstructure results in higher strength and toughness, while a coarse and uneven microstructure results in lower strength and toughness.
D. Surface finish of alloy steel
The surface finish of alloy steel affects its ability to resist breaking, especially in applications where fatigue is a concern. Rough surfaces or surface defects can act as stress concentrators, leading to premature failure of the steel. Therefore, proper surface preparation and finishing are critical in preventing the breaking of alloy steel.
E. External factors like temperature and stress
External factors such as temperature and stress can also affect the ability of alloy steel to resist breaking. High temperatures can cause the microstructure of steel to degrade, leading to reduced strength and toughness. Stress concentrations, such as those caused by bending or welding, can also lead to premature failure of the steel. Therefore, it is essential to consider these external factors when selecting the appropriate type of alloy steel for specific applications.
Understanding the factors that affect the ability of alloy steel to resist breaking is crucial in ensuring its reliable performance. By considering these factors, engineers and designers can select the appropriate type of alloy steel for specific applications and ensure that it can withstand the stresses it will encounter.
By Huaxia-steel – Alloy Steel Suppliers
V. Common Reasons for Alloy Steel to Break
Alloy steel is known for its strength and durability, but it is not completely immune to breaking. There are several reasons why alloy steel may break, and understanding these reasons can help prevent breakage and ensure the safety of structures and equipment that use alloy steel.
A. Fatigue Failure
Fatigue failure occurs when a material is subjected to repeated loading and unloading cycles. This can cause small cracks to form in the material, which can eventually lead to a catastrophic failure. In alloy steel, fatigue failure can occur due to cyclic loading or stress caused by vibration or other mechanical forces. Proper design and maintenance can help prevent fatigue failure in alloy steel structures and equipment.
B.Overloading
Overloading occurs when a material is subjected to a load that exceeds its capacity. In alloy steel, overloading can cause the material to deform or even break. Overloading can occur due to improper use of equipment or structures, or due to unexpected changes in the load. Proper design and testing can help prevent overloading in alloy steel structures and equipment.
C. Environmental Factors like Corrosion
Environmental factors like corrosion can weaken the material and make it more prone to breaking. Corrosion can occur due to exposure to chemicals, moisture, or other environmental factors. Alloy steel is often used in harsh environments, and proper protection and maintenance can help prevent corrosion-related breakage.
D. Manufacturing Defects
Manufacturing defects can occur during the production of alloy steel, leading to weak spots or other weaknesses in the material. These defects can cause the material to break under stress, even if the stress is within the material’s capacity. Quality control measures can help prevent manufacturing defects in alloy steel.
E. Human Error
Human error, such as improper use or maintenance of equipment or structures, can also cause alloy steel to break. Proper training and maintenance procedures can help prevent human error-related breakage.
Understanding the common reasons for alloy steel to break can help prevent accidents and ensure the safety of structures and equipment that use alloy steel. Proper design, maintenance, and testing can help minimize the risk of breakage and ensure the long-term durability of alloy steel structures and equipment.
By Huaxia-steel – Alloy Steel Suppliers
VI. Prevention and Repair of Alloy Steel Breaking
Preventing alloy steel from breaking is crucial in ensuring safety and avoiding costly repairs or replacements. Here are some preventative measures that can be taken:
A. Proper Design and Maintenance
The design of alloy steel structures or components should take into account the intended use and potential stress factors. Regular inspections and maintenance should be performed to detect any signs of wear and tear, corrosion, or other issues that may compromise the strength and durability of the material.
B. Repair Methods like Welding and Annealing
If an alloy steel component has been damaged or broken, it may be possible to repair it through welding or annealing. Welding involves joining broken pieces of alloy steel using heat and filler material, while annealing involves heating the material to a specific temperature and then slowly cooling it to relieve internal stresses.
C. Replacement Options if Repair is not Possible
In conclusion, understanding the factors that affect the strength and durability of alloy steel, as well as common reasons for breaking, is crucial in preventing failures and ensuring safety in various applications. Proper design, maintenance, and repair methods can help extend the life of alloy steel components and structures, while replacement options may be necessary in cases where repair is not possible.
By Huaxia-steel – Alloy Steel Suppliersa
VII. Conclusion
In conclusion, understanding the strength and toughness of alloy steel is crucial to prevent it from breaking easily. Alloy steel is a popular material for many industrial applications due to its high strength and durability, but it is also prone to breaking if not properly maintained and used. Factors such as chemical composition, heat treatment process, microstructure, surface finish, and external factors like temperature and stress can all affect the ability of alloy steel to resist breaking.
Common reasons for alloy steel to break include fatigue failure, overloading, environmental factors like corrosion, manufacturing defects, and human error. To prevent and repair alloy steel from breaking, it is important to implement proper design and maintenance practices, use appropriate repair methods such as welding and annealing, and consider replacement options if repair is not possible.
Using high-quality alloy steel in applications where strength is crucial is important to ensure safety and reliability. Future developments in alloy steel technology may lead to even stronger and more durable materials that can withstand extreme conditions and prevent breaking. By understanding the factors that affect the strength and toughness of alloy steel, we can work towards improving the performance and reliability of this important material.
By Huaxia-steel – Alloy Steel Suppliers
Related Blogs
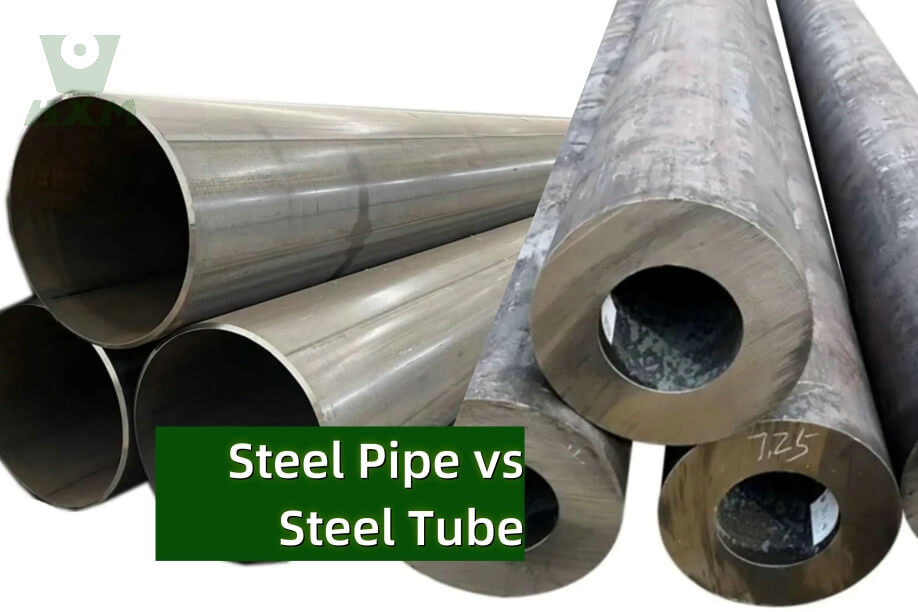
Steel Pipe vs Steel Tube: Key Differences and Applications
Discover the key differences between steel pipes and steel tubes, including their uses, measurements, and schedules like schedule 40 vs schedule 80 pipes. Learn which is right for your project and how to choose the best steel solution.
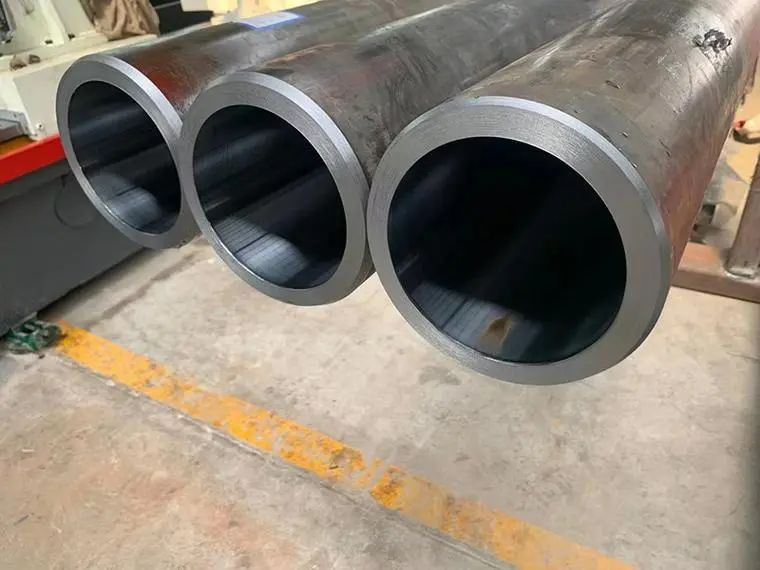
General Materials of Honed Tubes
Honed tubes are typically made from materials such as carbon steel, alloy steel, stainless steel, and special alloys. Carbon steel, like ST52 and 45#, is widely used for its strength and affordability, making it ideal for hydraulic and pneumatic systems. Alloy steel, including grades like 16Mn and 27SiMn, offers enhanced wear resistance and strength for high-pressure applications. Stainless steel, such as 304 and 316, is favored for its corrosion resistance, especially in harsh environments. Special alloys like Inconel and Hastelloy are used in extreme conditions where high temperatures or corrosion resistance is essential, such as in marine and chemical industries.
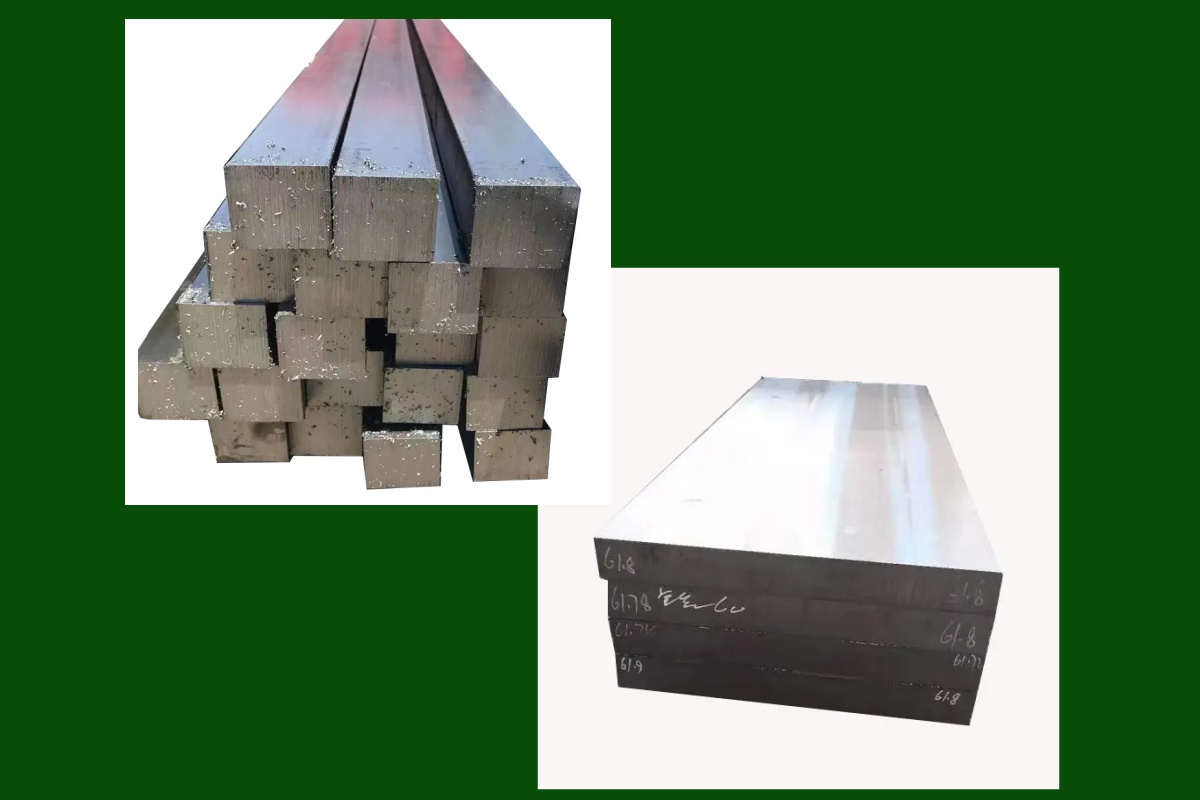
The Relationship Between Carbon Steel and Tool Steel
Carbon steel and tool steel are two fundamental types of steel, each with its own specific properties and applications. While they share some similarities—both being forms of steel with varying carbon content—they serve very different purposes in industrial and manufacturing contexts. Understanding the relationship between carbon steel and tool steel can help clarify their unique roles and why each is chosen for specific applications.
Table of Content
Request A Free Quote
We’d like to work with you
By Huaxia-steel – Alloy Steel Suppliers
If you require further information about our metal sheet products or architectural projects, please don’t hesitate to leave your contact details and message here.
Our team of experts will respond within 24 hours to continue the discussion and provide you with any additional information you requires.