Knowledge: What is tool steel?
Jacob was a young engineer with a passion for designing and building machines that could change the world. One day, he received a mysterious package in the mail from his mentor, a renowned inventor who had always inspired him. Inside the package was a small piece of metal, unlike anything Jacob had ever seen before. It was hard, dense, and seemed almost indestructible. His mentor had labeled it as ‘tool steel,’ and Jacob was immediately fascinated. He knew that this special metal could unlock a world of possibilities for his inventions. And so, he set out on a journey to explore the wonders of tool steel and uncover its secrets.
So a lot of people may ask,”What is too steel? “
Tool steel is a type of high-carbon steel that is designed for the production of tools, dies, and molds. It contains a higher amount of tungsten, molybdenum, or cobalt, which increases its strength, durability, and resistance to wear and heat. Tool steel can be classified into various grades based on their composition and properties, such as H13, D2, and A2. It is commonly used in manufacturing and engineering industries for applications that require cutting, drilling, shaping, or forming materials like metal, plastic, and wood.
Let me share with you more information about tool steel..
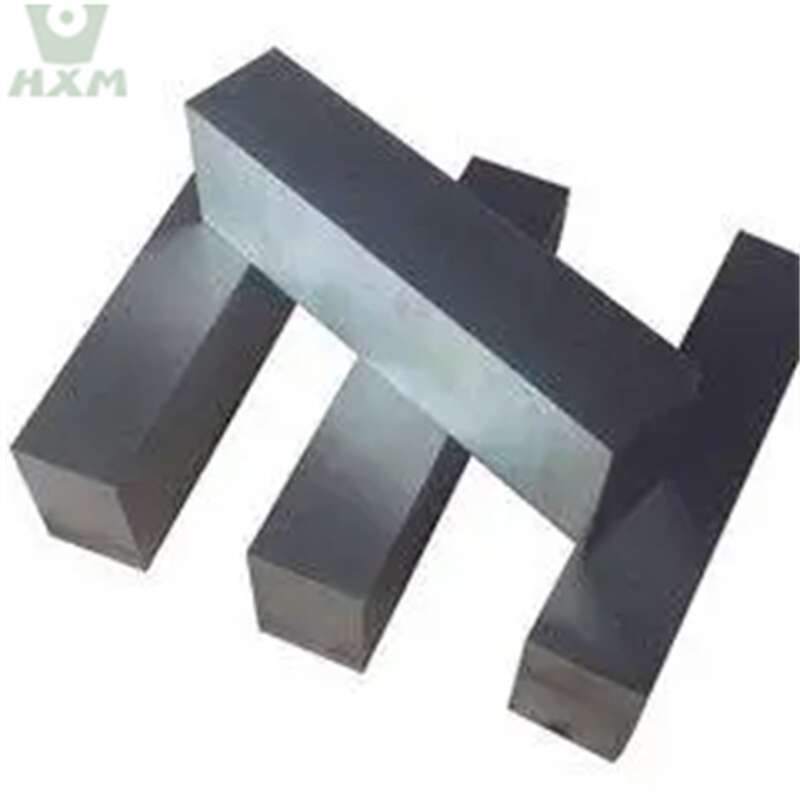
What are the different types of tool steel?
There are several types of tool steel, each with different properties and applications. Some common types include:
High-speed steel:
This type of tool steel contains tungsten, molybdenum, and other alloys that improve its heat resistance and hardness. It is commonly used in high-speed cutting tools such as drills, taps, and end mills.Cold-work steel:
This type of tool steel is used for applications that involve cutting and shaping materials at room temperature. It has high wear resistance, toughness, and hardness, and is used for making dies, punches, and molds.Hot-work steel:
This type of tool steel is used for applications that involve cutting and shaping materials at high temperatures. It has excellent thermal shock resistance, toughness, and strength, and is used for making forging dies, extrusion dies, and other hot-working tools.Shock-resistant steel:
This type of tool steel has high toughness and impact resistance, making it suitable for applications that involve sudden and heavy loads. It is commonly used in hammer dies, chisels, and other tools that are subjected to high impact loads.
How is tool steel different from other types of steel?
Tool steel is different from other types of steel in several ways. It is specifically designed for making tools, dies, and molds, and therefore has different properties than other types of steel. Some key differences include:
High carbon content:
Tool steel contains a higher percentage of carbon than other types of steel, which gives it its hardness and wear resistance.Alloying elements:
Tool steel often contains additional alloying elements such as tungsten, molybdenum, or cobalt, which improve its properties such as strength, toughness, and heat resistance.Specific properties:
Tool steel is designed to have specific properties such as high hardness, wear resistance, and toughness, which make it suitable for cutting, shaping, and forming materials.
What are the common applications of tool steel?
Tool steel is used in a variety of applications in the manufacturing and engineering industries. Some common applications include:
Cutting tools:
Tool steel is used to make cutting tools such as drills, milling cutters, and turning tools.Forming tools:
Tool steel is used to make forming tools such as dies, punches, and molds for shaping and forming materials.Machine components:
Tool steel is used to make machine components such as gears, bearings, and shafts that require high strength and wear resistance.Tooling systems:
Tool steel is used to make tooling systems such as tool holders, collets, and adapters that hold cutting tools and other tooling components.
What factors determine the performance of tool steel?
The performance of tool steel is determined by several factors, including:
Composition:
The composition of the tool steel, including the type and amount of alloying elements, determines its properties such as hardness, wear resistance, and toughness.Heat treatment:
The heat treatment process used to harden and temper the tool steel affects its properties such as hardness, toughness, and dimensional stability.Coatings:
Coatings such as TiN, TiAlN, and DLC can be applied to tool steel to improve its wear resistance and extend its tool life.Cutting conditions:
The cutting conditions such as cutting speed, feed rate, and depth of cut affect the performance of the tool steel by generating heat and wear.
What are the advantages and disadvantages of using tool steel?
Advantages of using tool steel include its high hardness, wear resistance, and toughness, which make it suitable for cutting, shaping, and forming materials. It also has good dimensional stability and can be machined to tight tolerances. However, tool steel is relatively expensive compared to other materials and can be brittle if not properly heat-treated. It can also be difficult to machine due to its high hardness and can require specialized equipment and techniques.
How is tool steel manufactured and processed?
Tool steel is typically manufactured using an electric arc furnace, which melts scrap steel and alloying elements together to form a new alloy. The molten steel is then poured into a mold and allowed to cool and solidify. The resulting ingot is then hot-rolled or forged into the desired shape and size. The tool steel is then heat-treated to achieve the desired hardness and toughness, and may be machined or ground to final dimensions.
What are the proper storage and handling practices for tool steel?
Proper storage and handling of tool steel is important to prevent damage and ensure optimal performance. Tool steel should be stored in a dry, clean, and well-ventilated area to prevent rust and contamination. It should be kept away from sources of heat and moisture, and should be protected from impacts and scratches. Tool steel should be handled with care to prevent chipping or other damage, and should be cleaned and inspected regularly to ensure its integrity.
What is the cost of tool steel compared to other materials?
Tool steel is generally more expensive than other materials such as carbon steel or aluminum, due to its higher alloy content and specialized manufacturing processes. The cost of tool steel can vary depending on the type and grade of the steel, as well as market conditions and other factors. However, the higher cost of tool steel is often offset by its superior performance and longer tool life, which can result in cost savings over time.
How does the composition of tool steel affect its properties?
The composition of tool steel, including the type and amount of alloying elements, can significantly affect its properties such as hardness, wear resistance, and toughness. For example, increasing the amount of tungsten in tool steel can improve its hardness and wear resistance, while increasing the amount of chromium can improve its corrosion resistance. The composition of tool steel is carefully balanced to achieve the desired properties for a particular application.
What is the role of tool steel in the manufacturing industry?
Tool steel plays a critical role in the manufacturing industry by providing the necessary cutting, shaping, and forming tools for a wide range of applications. From high-speed cutting tools for machining complex parts to dies and molds for forming and stamping materials, tool steel is essential to the production of a wide range of products. Tool steel is also used in the production of machine components such as gears and bearings, as well as tooling systems for holding and positioning cutting tools.
Conclusion
Tool steel is a specialized material used extensively in the manufacturing industry. It offers many advantages, such as high hardness, wear resistance, and toughness, making it suitable for cutting, shaping, and forming materials. However, it is relatively expensive compared to other materials and can be brittle if not properly heat-treated. Proper storage and handling practices are important to prevent damage and ensure optimal performance.
Tool steel is manufactured using an electric arc furnace, poured into molds, and hot-rolled or forged into the desired shape and size. It is then heat-treated and machined or ground to final dimensions. The cost of tool steel varies depending on type and grade, but its higher cost is often offset by superior performance and longer tool life.
The composition of tool steel affects its properties, with alloying elements such as tungsten and chromium used to improve hardness, wear resistance, and corrosion resistance. Tool steel plays a critical role in the manufacturing industry, providing cutting, shaping, and forming tools for a wide range of applications, as well as machine components and tooling systems for holding and positioning cutting tools.
Related Posts
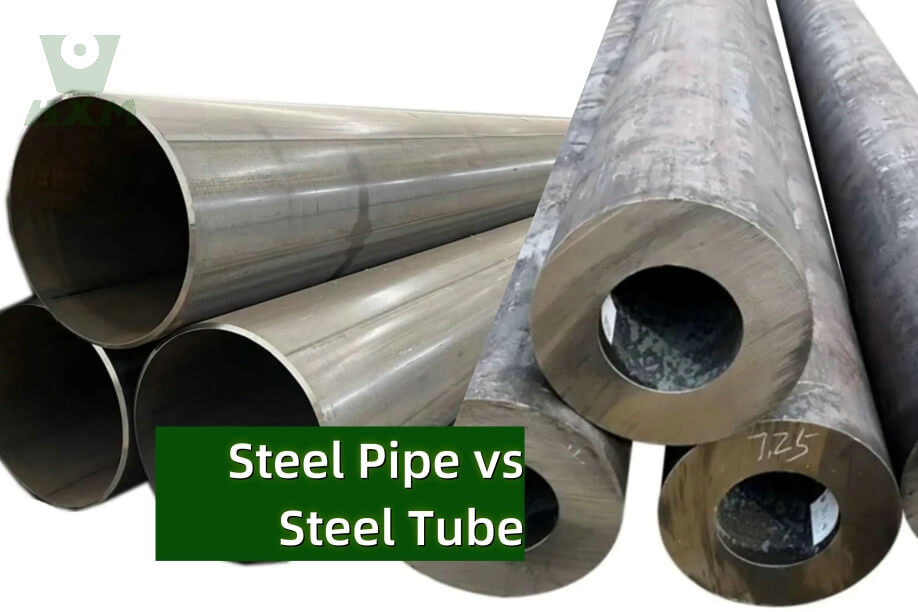
Steel Pipe vs Steel Tube: Key Differences and Applications
Discover the key differences between steel pipes and steel tubes, including their uses, measurements, and schedules like schedule 40 vs schedule 80 pipes. Learn which is right for your project and how to choose the best steel solution.
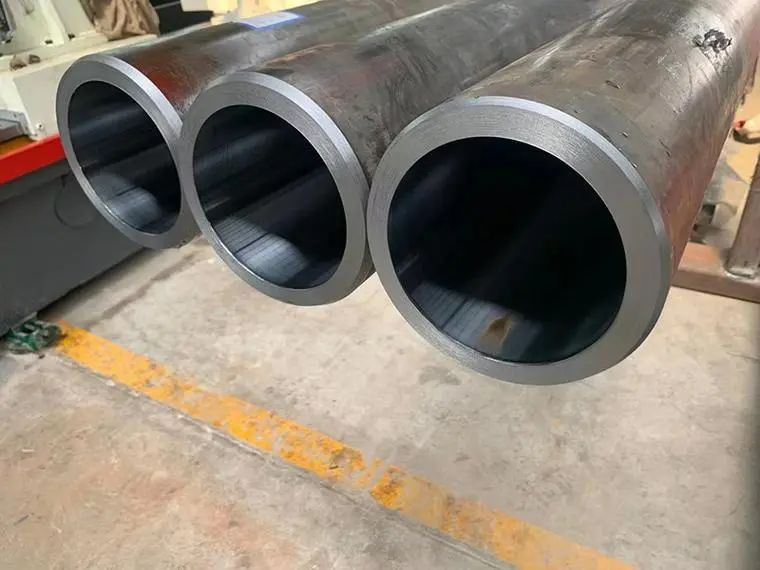
General Materials of Honed Tubes
Honed tubes are typically made from materials such as carbon steel, alloy steel, stainless steel, and special alloys. Carbon steel, like ST52 and 45#, is widely used for its strength and affordability, making it ideal for hydraulic and pneumatic systems. Alloy steel, including grades like 16Mn and 27SiMn, offers enhanced wear resistance and strength for high-pressure applications. Stainless steel, such as 304 and 316, is favored for its corrosion resistance, especially in harsh environments. Special alloys like Inconel and Hastelloy are used in extreme conditions where high temperatures or corrosion resistance is essential, such as in marine and chemical industries.
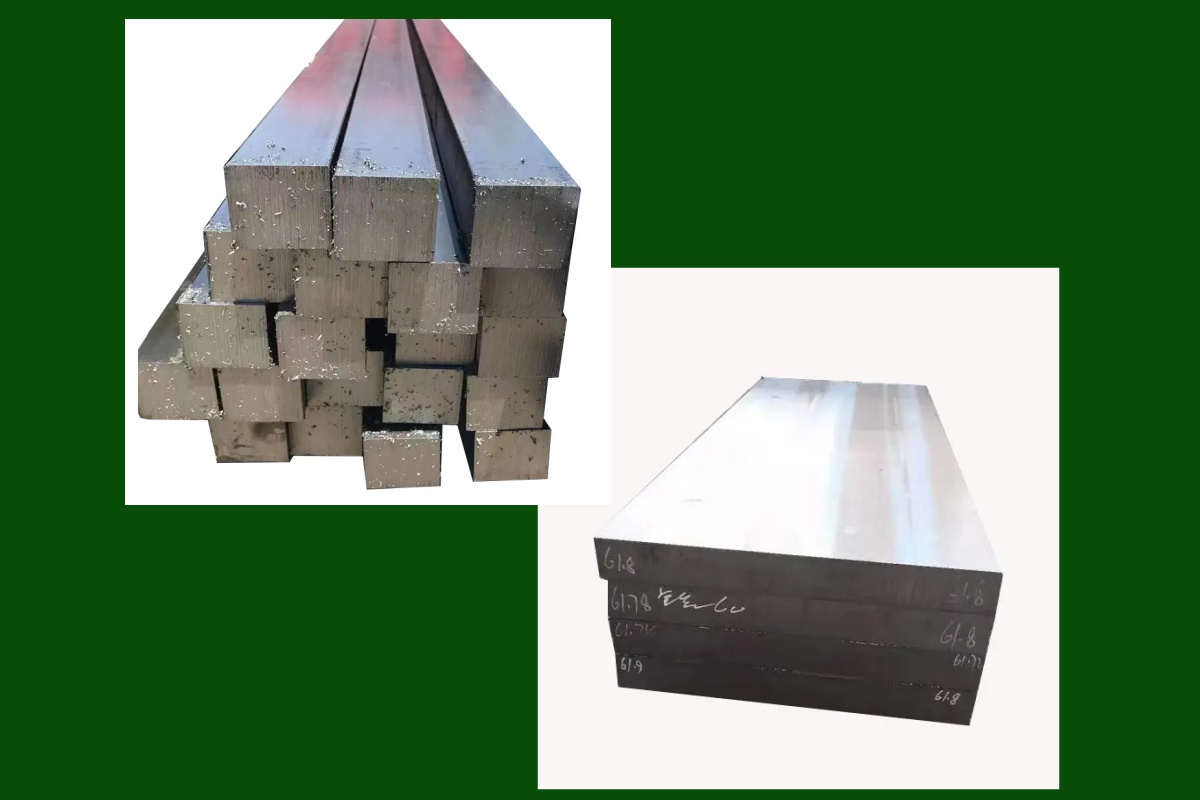
The Relationship Between Carbon Steel and Tool Steel
Carbon steel and tool steel are two fundamental types of steel, each with its own specific properties and applications. While they share some similarities—both being forms of steel with varying carbon content—they serve very different purposes in industrial and manufacturing contexts. Understanding the relationship between carbon steel and tool steel can help clarify their unique roles and why each is chosen for specific applications.
Table of Contents
Request A Free Quote
We’d like to work with you
If you require further information about our metal sheet products or architectural projects, please don’t hesitate to leave your contact details and message here.
Our team of experts will respond within 24 hours to continue the discussion and provide you with any additional information you requires.